Lagere voorraden door anders te meten
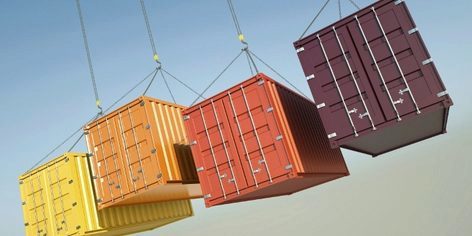
Voorraad planning en besturing vindt plaats met methoden die zijn ontwikkeld in de jaren zestig van de vorige eeuw, zonder dat deze mee ontwikkelen om kunnen omgaan met toenemende complexiteit in moderne supply chains. Meer producten met kortere productlevenscycli, meer internationale concurrentie en kortere levertijdverwachting bij klanten dragen eraan bij er vaak wijzigingen moeten worden aangebracht in planningen en prioriteiten. Dit leidt tot hogere kosten voor extra omstellen van machines, extra overuren en extra kosten voor spoedzendingen. Het gevolg hiervan is een verslechtering van de ROI.
Wat zijn de huidige problemen met forecast gestuurde productie? En kan Demand Driven MRP-planning aan deze bezwaren tegemoet kan komen?
Auteur Derk Kuiper is eigenaar van Visie Partners B.V.
Financieel managers en controllers sturen al decennialang op reductie van voorraden. Maar hoe effectief is dit streven? Werkt het wanneer we sturen op uitkomsten zonder de processen te begrijpen? Hebben we de juiste prestatie indicatoren om de processen beter te besturen? En welke nieuwe inzichten zijn er om voorraad op een verantwoorde manier te verlagen?
Sinds jaar en dag wordt er gebruik gemaakt van kengetallen als omloopsnelheid van voorraad, oftewel hoeveel keren in een jaar wordt de voorraad gemiddeld genomen omgezet? Hoe effectief is dit kengetal wanneer het is gebaseerd op de voorraad op balansdatum, ofwel een dag per jaar? Veel bedrijven hebben alleen op balansdatum lage voorraden en de rest van het jaar ligt de voorraad gemiddeld genomen veel hoger. Deze hogere voorraad heeft tot gevolg dat de omloopsnelheid in werkelijkheid lager is dan uit de meeste jaarverslagen blijkt. Maar toch blijven veel bedrijven sturen op een tijdelijke kunstmatig lage voorraad. Dit is geen voorraadmanagement, maar management van cijfers.
Verder maken zeer veel bedrijven gebruik van de formule van Camp (economische bestelhoeveelheid) voor het berekenen van de optimale bestelgrootte voor inkooporders en productieorders. Deze formule, die meer dan 100 jaar geleden is ontwikkeld door zijn naamgever, geeft de schijn van een exacte uitkomst van de optimale bestelhoeveelheid. Deze uitkomst mag dan exact zijn, hij is vaak vooral exact fout. Theoretisch kun je de bestelkosten en de voorraadkosten tegenover elkaar zetten en exact bereken wat het laagste kostenpunt is, ofwel de meest economische bestelhoeveelheid. Alleen zijn de bestelkosten vaak niet per product/per order bekend en ook niet constant door het jaar heen. Dit geldt ook voor de kosten per product van het aanhouden van voorraad. Naast het feit dat voorraadkosten doorgaans niet bekend zijn, blijven andere kosten buiten beschouwing.
Denk hier bijvoorbeeld aan de voorziening incourant die vooral een exercitie is tijdens het opmaken van de jaarrekening, maar die niet wordt terugvertaald naar voorraadkosten per product. Dit geldt ook voor de vergoeding voor kapitaalkosten, die (als die al wordt meegenomen) wordt gebaseerd op de (te lage) gemiddelde voorraad op balansdatum.
Voorraad is niet alleen kapitaalbeslag en een kostenpost, maar vervult ook een goede functie. Voorraad wordt natuurlijk aangelegd om aan de vraag te kunnen voldoen, voor het opvangen van vraagvariatie (veiligheidsvoorraad) en voor het bevorderen van de doorstroming (flow) in het productieproces.
Leverbetrouwbaarheid (customer service)
Op basis van een vraagvoorspelling (forecast) wordt bepaald hoeveel product er nodig is om aan de vraag te voldoen. Omdat de doorlooptijd van de meest logistieke processen nogal lang kan zijn, moet je ruim op tijd weten wat je moet gaan produceren en (nog verder terug) welke grondstoffen je moet gaan inkopen. Maar zoals iedereen weet komen voorspellingen nooit uit en is er altijd een foutmarge. De meeste bedrijven echter gaan iedere dag opnieuw berekenen hoeveel de vraag voor de nabije toekomst zal zijn en op basis daarvan wordt ingekocht en geproduceerd. Maar wanneer de doorlooptijd in de productie bijvoorbeeld acht weken is en de schatting van de vraag naar het eindproduct in week 4 wordt herzien, dan is er een probleem. We moeten dan inkoop en productieorders gaan met hoge spoed laten leveren of gaan produceren om op tijd klaar te zijn om deze nieuwe deadlines te halen. Dit gaat gepaard met extra transportkosten om zaken snel binnen te hebben en overwerk voor mensen in de productie. Als er al een KPI is voor de betrouwbaarheid van het productieproces is dat productie ten opzichte van plan. Maar hoe zinvol is deze KPI als het plan steeds wijzigt? Het zou veel beter zijn om het plan stabieler te houden en niet iedere dag weer helemaal opnieuw berekenen.
Veiligheidsvoorraad (Safety stock)
Algemeen wordt voor veiligheidsvoorraad de (vrij vertaalde) APICS-definitie aangehouden: Voorraad die wordt aangehouden om variatie in vraag of aanbod op te vangen. Met de definitie is niets mis, maar wel hoe er in de dagelijkse praktijk van voorraadplanning mee wordt omgegaan. ERP (Enterprise Resource Planning) systemen gebruiken de veiligheidsvoorraad in werkelijkheid niet om schokken op te vangen. Wanneer je bijvoorbeeld voor een bepaald halffabricaat een veiligheidsvoorraad hebt van 100 stuks en het verwachte voorraad niveau aan het einde van een bepaalde week zou 97 stuks bedragen, dan maakt het MRP (Material Requirements Planning, onderdeel van ERP) een order aan om dit voorraadtekort op te vangen. Eigenlijk fungeert dit weer als een nieuw bestelniveau van 100 in plaats van 0, ingeval je geen veiligheidsvoorraad hebt. Deze orders worden vervolgens vertaald naar andere geproduceerde items die nodig zijn als input in productie en van daaruit weer naar ingekochte grondstoffen. Ook hier geldt hetzelfde als hierboven staat aangegeven voor verwachte verkoopaantallen. In de praktijk worden er geen KPI’s gebruikt om te meten wat de effectiviteit van veiligheidsvoorraad is. Wel is er de afgeleide meting van customer service (leverbetrouwbaarheid). Als deze te laag wordt, is de algemene reflex dat de veiligheidsvoorraad omhoog moet, omdat deze ogenschijnlijk onvoldoende bescherming heeft kunnen geven. Ook komt het voor dat er wordt getracht om nog gedetailleerder te gaan forecasten.
Belang van Flow
Flow in productie en logistieke processen wordt bedreigd door variatie in processen. Gemiddelde capaciteit van een aantal achter elkaar opgestelde machines of productieafdelingen zegt niets over het geproduceerde aantal producten. Dit wordt veel meer bepaald door de spreiding rondom de gemiddelde capaciteit. Op basis van deze spreiding zou je moeten kijken naar de posities in het proces waar variatie de doorstroming kan verstoren. Veel bedrijven kennen het opslinger (bullwhip) effect, waarbij opeenvolgende bronnen van variatie de neiging hebben elkaar exponentieel te versterken met het aantal stappen in het productieproces. Dit effect doet zich echter ook voor bij processen in de supply chain.
Wanneer we op de juiste plaatsen buffers neerleggen om variatie op te vangen kan dit leiden tot meer onderhanden werk op sommige posities, maar tot lagere voorraad op andere plaatsen in de stroom van productieactiviteiten. In totaal zal de voorraad lager worden omdat het zichzelf versterkende bullwhip effect, bij het voorraadpunt wordt gestopt.
Om te bepalen of voorraad zijn functie tussen productie en verkoop goed vervult, gebruiken we de term customer service. Customer service-levels worden uitgedrukt in een percentage, bijvoorbeeld 95%. Dit betekent dat het product (of bestelling) in minimaal 95% van de bestellingen volledig en op tijd aan de klant wordt geleverd.
Voorraad staat op de balans met de categorieën grondstoffen, onderhanden werk en gereed product. Het gereed product is dat wat beschikbaar is om te leveren naar de klant.
Sinds de introductie van MRP-planning software 50 jaar geleden is er nogal wat veranderd in de dynamiek van organisaties en supply chains. Denk hierbij aan grotere diversiteit aan producten, steeds kortere productlevenscycli, toegenomen concurrentie en meer dynamiek op verkoop- en inkoopmarkten en langere aanvoerlijnen voor veel producten. Deze ontwikkelingen brengen een toename van onzekerheid met zich mee voor de voorraad planning. Dit leidt tot telkens meer moeten opjagen met spoed orders (expediting) of vertragen (de-expediting) om de weg vrij te maken voor spoed orders. Dit vergt een herplanning van orders in productie en in het voorraadproces. Dit gaat gepaard met extra kosten, verlies van productiecapaciteit en extra hoge voorraden. Veel bedrijven zien dit terug in te hoge voorraad van materialen die ze op een specifiek moment niet meer nodig hebben, terwijl er op hetzelfde moment tekorten zijn van anderen.
Oud Paradigma: kosten per product
Algemeen aanvaarde waarheid is dat de kostprijs per product zo laag mogelijk moet zijn om voldoende winst te kunnen maken. Om die reden worden bijvoorbeeld producten gemaakt in batches om te zorgen dat de kostprijs per product zo laag mogelijk is. Grotere batches leiden tot lagere kosten per geproduceerd product omdat de vaste kosten over een groter aantal kosten kunnen worden verdeeld. Lagere kosten per product leiden weer tot een hogere winst. Het streven naar zo laag mogelijke kosten per product worden dan vertaald naar de KPI’s voor bijvoorbeeld productiemanagers, gericht op activiteiten die ‘waarde toevoegen’. Door de focus op grotere batches ga je de verschillende producten ook minder vaak produceren. Met andere woorden de product mix interval wordt groter. Dus moet je verder in de toekomst kijken voor de schatting van de benodigde productie aantallen. Maar hoe verder je in de toekomst moet kijken voor een vraagvoorspelling hoe meer onzekerheden er zijn. Meer onzekerheid leidt dan weer tot meer veiligheidsvoorraad om de servicelevels te halen. Dit leidt tot hogere voorraden.
Belang van flow
Probleem is dat je niet direct kunt sturen op financiële uitkomsten, maar dat je daarvoor de juiste beslissingen nemen bij de inrichting van de logistieke besturingsprocessen. Als je een hogere omloopsnelheid wilt hebben van je voorraden, dan zullen de processen allemaal gericht moeten zijn om doorstroming (flow).
Doorstroming kun je verbeteren door op strategische posities in productstructuur voorraad neer te leggen waar deze voorraad nut heeft voor de bevordering van de goederenflow. Neem als voorbeeld drie machines op een rij die allemaal gemiddeld 100 output per uur kunnen genereren. Veronderstel dat er een variatie is rond het gemiddelde die verschillend is voor deze machines. Dus zul je buffers moeten aanleggen die de variatie absorberen, waardoor er voldoende doorstroming komt. Als je geen buffers aanlegt, zal je geen 100 output kunnen halen. Moet je dan overal buffers tussen leggen? Nee, maar wel daar waar dit het meest bijdraagt aan flow.
Oud Paradigma: Standaard kostprijs
Probleem met de standaardkostprijs is dat deze niet helpt bij het genereren van flow (werkkapitaalverlaging) en gelijktijdige resultaatverbetering. Stel je hebt een bottleneck in een productieproces, waardoor de vraag naar producten/componenten groter is dan de capaciteit. De capaciteit van de bottleneck zal dan bepalend zijn voor de hoeveelheid die uit het hele productieproces komt. Je zult dus moeten kijken naar welke producten je moet gaan maken om zoveel mogelijk winst uit de bottleneck te halen. Op korte termijn zijn de meeste arbeidskosten en overheadkosten vast. Dus het product met het grootste verschil tussen omzet en de echte variabele kosten per product zijn relevant. Deze echte variabele kosten zijn in ieder geval de grondstoffen en materialen die je gebruikt en in zeer weinig gevallen zullen lonen op korte variabele zijn. Vervolgens moet je kijken naar het beslag wat ieder product legt op de bottleneck. Vervolgens geef je prioriteit aan het product met de hoogste bijdrage per productie-eenheid (bijvoorbeeld minuten) van de bottleneck. Wanneer je weet wat je wilt produceren zul je vervolgens moeten gaan sturen op voldoende doorstroming in de bottleneck. Dit kan door voorraad buffers of tijdbuffers voor de bottleneck te leggen om te zorgen dat deze nooit zonder materiaal komt te zitten. Dus hier gaat het om het beschermen van flow om de totale output van het productieproces te beschermen.
Demand Driven Planning
Het probleem van traditionele denkmodellen en prestatie indicatoren is dat ze de valse illusie geven dat je sturing geeft aan processen en voorraden. Dit kan echter alleen het geval zijn wanneer je dynamische planning hebt en regelmatig de omvang van ordergroottes, plaats en omvang van buffers en de prioriteiten in de planning aanpast aan de ontwikkelingen. Demand Driven MRP (DDMRP) is een methode van plannen en sturen van orders, capaciteit en voorraadbuffers om te zorgen dat er ongestoord kan worden gewerkt. DDMRP is een methode die een aantal elementen uit Lean, Six Sigma, Theory of Contraints (Bottlenecks), MRP op een innovatieve manier samensmeedt.
Kritisch in het gebruik van DDMRP is de bepaling van de strategisch positionering van grondstoffen en halffabricaten in de productstructuur en de in de bewerkingsprocessen. De volgende punten voor bufferlocaties kunnen worden overwogen:
a. Bottlenecks in productieproces
b. Voorraad eindproduct
c. Voorraad basis grondstof
d. Gedeelde resources
Voordelen DDMRP
DDMRP komt tegemoet aan alle hiervoor genoemde bezwaren van de traditionele wijze van werken. Werken met DDMRP kan een besparing op voorraad kan een besparing op voorraad opleveren van 20% tot 40%, tegen lagere kosten. De besparing van kosten zit enerzijds in de lagere voorraadkosten, die veelal meer dan 30% zijn van gemiddelde voorraadwaarde, maar ook uit minder kosten van spoedleveringen (luchtvracht voor eindproducten, minder overwerk en minder ingrepen in het lopende productieproces etc.). Verder kan er meer capaciteit beschikbaar komen door kennis van bottlenecks te gebruiken voor het produceren van de juiste (meest winstgevende) producten.
Conclusie
Traditionele financiële prestatie indicatoren zoals ROE zijn goed voor analyse maar niet om te sturen. Voor financiële beslissingen moet alleen worden gekeken naar de kosten die relevant zijn voor de beslissing die op dat moment wordt genomen. Dus alleen echte variabele kosten meenemen voor korte termijn beslissingen over huidige orders en prioriteitstelling. Naarmate de beleidshorizon langer wordt, kunnen meer kosten als variabel worden aangemerkt, ofwel Different Costs for Different Purposes. Wil je voorraden verlagen, dan heb je doorstroming (flow) nodig. Om de flow te kunnen opvangen moet je op kritische punten in het proces buffers aanleggen die dynamisch worden aangepast aan veranderingen in vraag en variatie en doorlooptijd.